Know About Distillation Process of Crude Oil
The refinement of crude oil begins with its distillation, but very few of the components that come from that process are ready for the open market. As an example, only forty per cent of the total crude oil when it is distilled is gasoline, although one of the major products that comes from this process is gasoline.
The pyrolysis oil distillation plant is what separates the different substances from the crude into what can be useful, and this is the most important step in the process of refinement.
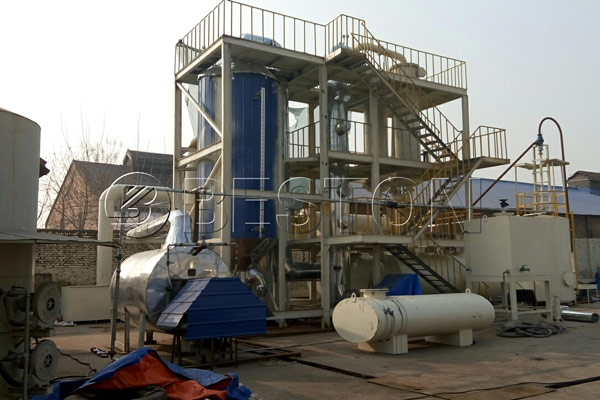
The process begins by heating the crude oil mixture to very high temperatures, and this heating is usually done with steam that is applied to a very high pressure at temperatures of around 1112 degrees Fahrenheit. In this process, the mixture will boil forming a bapor, or gases.
The vapor will then enter the bottom of a long column, and this column is called the fractional distillation column, which is filled with plates, or trays. The trays have many holes or bubble caps, a lot like caps on a soda bottle that are loose. This allows the vapor to pass through, with a difference in temperature from the bottom to the top – hotter at the bottom and cooler the closer you get to the top. Get more information about the portable pyrolysis machine here.
When the material in the vapor reaches a certain height where the temperature in the column equals that material’s boiling point, it condenses back into a liquid from a vapor state, and it is collected by the various trays at that height. This is called fractional distillation and it serves to separate different substances within the crude oil itself. The plant can also turn waste plastic to diesel.
Since gasoline is 40% of distilled crude oil it is a major product of the crude oil. So rather than continually having to distill larger quantities of crude oil to get gasoline, oil refineries process the products from distillation chemically to make the gasoline, which increases the gasoline yield from each barrel of crude.
Petroleum refineries are very large complexes of processing units, storage tanks and myriads of pipes, refining columns and machinery. Each refinery has its own specific setup and its combination of processes. This is mainly determined by the location of the refinery, the economics of the situation, the actual products that are desired, and space available. There are undoubtedly no two refineries that are identical in every aspect.
The capacity of larger refineries huge in that some can process as much as 800,000 to 900,000 barrels of crude oil per day. The main end-products that come from the process of tyre pyrolysis oil distillation plant can be grouped into three categories: https://www.bestongroup.com/plastic-to-diesel-plant-cost/.
The second category are the middle distillates which includes diesel fuels for rail and auto usage, kerosene, heating fuel for residential use and other light fuel types.
The third category are the heavy distillates which include the heavy fuel oil types, and other residual fuel oils, and octane items.
The distillation process is a vital process in the refining and creation of the many by-products created from crude oil.
If you want to know more details about the process of crude oil distillation, please click on this website.